The problems associated
with molecular and particle contamination of spacecraft components,
instruments and structures are well known and documented especially
those that contain fine mechanisms and/or optics. This problem is
severely exaggerated when the instrument is operating under space
vacuum. When looking at contamination problems in a space environment
there are two important contamination sources:
Particulate
contamination.
Particulate contamination
is basically the dust and other particles that is always present in
our earth environment. Added to this other forms of contamination
may also be present e.g. hair, skin particles etc.
Molecular contamination.
Molecular contamination
in a space vacuum is bought about by the out gassing of materials
used in the manufacture of the instruments and/or structures. Other
significant molecular contamination sources found in the Earth environment
(at atmospheric pressure) can be broadly grouped into four categories.
These are:
- Acids - A corrosive
material with a chemical reaction that of an electron acceptor.
- Bases - A corrosive
material with a chemical reaction that of an electron donor.
- Condensables
- (excluding water) boiling point above room temperature at atmospheric
pressure
- Dopants - A
chemical element which is capable of modifying the electrical properties
of a semi conductive material
In order to keep
both forms of contamination to a minimum strict cleanliness controls
are maintained throughout all stages of production, assembly, test
and integration and in the case of molecular out gassing, rigorous
material selection and monitoring of contamination levels within the
cleanroom using various methods.
To this end M.S.S.L
make use of an on site class 100 laminar flow clean facility. Its
design specification is such that cleanliness levels conform to the
U.S Fed. Standard 209E. The cleanroom is validated every 6 months
by an independent external contractor.
Description.
The M.S.S.L cleanroom
is based upon the horizontal laminar flow design, with one complete
end wall being a bank of HEPA (High Efficiency Particle Air) filters.
The efficiency of the HEPA filters are rated at 99.997% for 0.1 micron
diameter particles. The exhaust return air is recirculated via a room
width filter bank in the ceiling at the opposite end of the HEPA filters.
The ratio of recirculated air to fresh air intake is: 75% recirculated
air and 25% fresh air intake. Additionally the fresh air intake is
fitted with a fine dust pre filter and LUWA AFP gas adsorption filters
capable of filtering most Airborne molecular contaminants. This ensures
the cleanroom is isolated from external contamination events and has
resulted in the MSSL cleanroom having an extremely low background
AMC level. Details of background contamination levels can be found
here.
HEPA filters.
HEPA filters cannot
reduce the amount of contamination (both particulate and molecular)
introduced downstream of the filter. The primary sources of downstream
contamination
come from:
- A person
sitting generates about 100 000 particles per cubic foot
- Sitting down
or standing up generates about 2 500 000 particles per cubic ft
- Walking generates
about 10 000 000 particles per cubic ft
- Grinding,
sweeping, welding (including soldering) adds billions of particle
per cubic ft
- Two surfaces
rubbing generates billions of particles per cubic ft
- An open,
non-air locked door can add billions of particles per cubic ft
- Process equipment
add particles
- Process materials
add particles
- Maintenance
activities add particles
- Construction
residue can generates massive particles
- Silica gel
can add billions of particles per cubic ft.
Thus the overall
contamination control of the M.S.S.L. clean facility not only depends
on the filtration system, but also depends upon the management of
processes and activities that are introduced in the clean facility.
The filtered air is temperature and humidity controlled to 19 deg
C +- 1 deg C and 50 % Relative Humidity (RH) +-5%. These values are
continuously monitored and recorded.
Cleanroom design/layout
The cleanroom
is divided along its length in ratio 2:1 by a light proof stud partition.
This provides two completely separate cleanrooms. The layout of the
cleanroom is shown below. The larger of the two rooms is a conventional
cleanroom and is known as the white cleanroom. The smaller room is
completely blackened and light proof and is known as the dark cleanroom.
The dark cleanroom is primarily used for optical work and was used
for both the XMM
Optical monitor and SWIFT
UVOT assembly,optical alignment and testing activities.
The white cleanroom
is divided into 3 zones, A, B and C. Zone A is located long the entire
length of the HEPA filters and is the cleanest area of the cleanroom.
Zone B is located in the centre of the cleanroom and zone C is at
the entrance to the cleanroom. In practice, due to the design of the
cleanroom Zone C will always be the more "contaminated" of the three zones. In practical terms zone A is usually well below
100 particles per cubic ft @ 0.3 micron diameter particles, but is
also dependent on activity. The same applies to the other zones. There
are two laminar flow benches located in the M.S.S.L. cleanroom, one
is sited in zone B in the white cleanroom and the other is situated
in the dark cleanroom in zone C. Both these laminar flow benches rate
consistently with Class 10 (F.S 209E) or better.
External to the
cleanroom is the Anteroom. The Anteroom has double doors with weighted
grills to maintain over pressure in the Anteroom. These doors open
directly into the cleanroom. If the doors in the Anteroom that lead
into the cleanroom are opened at the same time as the doors to the
entrance of the Anteroom then an audible alarm will be sounded. The
Anteroom is used to change into and out of cleanroom garments.
Cleanroom Layout.
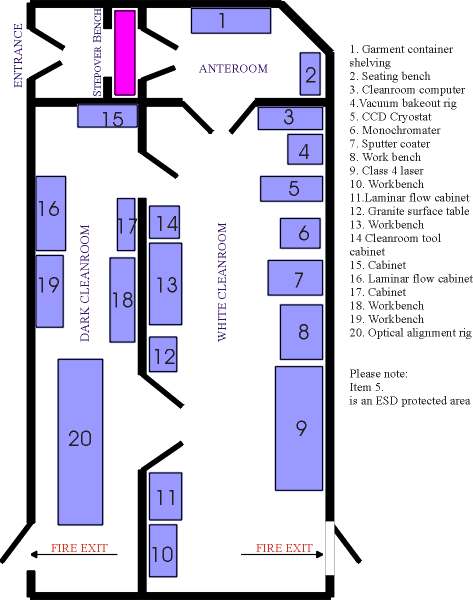