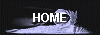
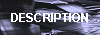
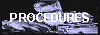


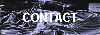
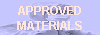
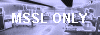
|
Cleaning procedures for clean areas used in the assembly, test and integration of flight hardware
An Acrobat pdf version of these procedures can be downloaded here
Contents
Introduction
In order to meet project contamination cleanliness requirements, cleanrooms, laminar flow benches and flight hardware work surfaces need to be cleaned at regular intervals so that surface contamination levels are minimised and the possibility of contamination redistribution is significantly reduced. This document covers the cleaning procedures for clean areas used in the assembly, integration and test of flight hardware at MSSL.
Required Materials
- Two Buckets: Polyethylene, Polypropylene, or Stainless Steel
- Solution: Filtered De Ionised water with Cleanroom Detergent
- Isopropyl Alcohol (IPA) – Spectro grade only
- Critical neutral detergent
- Mop/Squop: with stainless steel handle and PVA, nylon, cellulose or polyurethane sponge
- Cleanroom Vacuum: HEPA-filtered
- Cleanroom Wipes: Lint-free Polyester
The following procedure shall be used for clean area maintenance:
Clean Benches
- Clean benches shall be cleaned before initial use and as needed thereafter
- With a HEPA-filtered vacuum cleaner, vacuum areas with excessive particle accumulations on the clean bench exterior. Repeat until visible particles have been removed
- Use a powerful (100W) white light source and view the surface at an acute angle to determine surface particulate cleanliness. Use a black light source (UV) to show up possible molecular contaminants. Oils, greases, finger prints etc will show up under Black light inspection as fluorescence. Any evidence of fluorescence shall be cause for recleaning. If recleaning does not reduce the fluorescence, an investigation shall be made to determine whether the fluorescing material is contamination or the basic material
- After vacuuming the clean bench exterior, vacuum the clean bench tabletop until surfaces are free of visible particles. Do not overlook recesses in clean bench surfaces
- Inspect exterior clean bench surfaces for visible residue. If residue is found, remove by wiping the areas with a cleanroom wipe that has been lightly dampened with IPA. Repeat until the surface is free of visible residue
- Solvent wipe clean bench table top surfaces with cleanroom wipes that have been lightly dampened with IPA. During solvent wiping, wipe surfaces in a unidirectional manner and fold the wipe or obtain a new wipe when the wiping surface appears contaminated. Do not dip wipes in the solvent container
- Repeat until table top and used wipe surfaces do not display visible residue
Laminar flow benches
- Laminar flow benches shall be cleaned before initial use and as needed thereafter
- Start the cleaning and inspection process at the HEPA filter end of the laminar flow bench and work towards you
- Using a HEPA-filtered vacuum cleaner, vacuum all horizontal and vertical surfaces of the laminar flow bench, making sure that all loose particles are removed from recesses and corners
- Use a powerful (100W) white light source and view the surface at an acute angle to determine surface particulate cleanliness. Use a black light source (UV) to show up possible molecular contaminants. Oils, greases, finger prints etc will show up under Black light inspection as fluorescence. Any evidence of fluorescence shall be cause for recleaning. If recleaning does not reduce the fluorescence, an investigation shall be made to determine whether the fluorescing material is contamination or the basic material
- Use critical neutral detergent and cleanroom polyester wipes to wet wipe all horizontal and vertical surfaces. Use a “pull and lift” method with the wipes, stroking in one direction only. Replace wipes after three cleaning strokes or fold wipe over and use a clean surface of the wipe
- Solvent wipe the laminar flow bench surfaces with cleanroom wipes that have been lightly dampened with IPA. During solvent wiping, wipe surfaces in a unidirectional manner and fold the wipe or obtain a new wipe when the wiping surface appears contaminated. Do not dip wipes in the solvent container. Repeat until the laminar flow bench and used wipe surfaces do not display visible residue
- Inspect the laminar flow bench walls and ceiling. If significant contamination is found clean the surfaces again using the above procedure
Cleanrooms
- Cleanrooms shall be cleaned a minimum of three times a week and the cleaning schedule increased as appropriate during periods of high activity
- Empty all trash cans if more than half full prior to starting the cleanroom cleaning process
- Start the cleaning and inspection process at the HEPA filter end of the cleanroom and work backwards to the entrance
- Use a powerful (100W) white light source and view the surface at an acute angle to determine surface particulate cleanliness. Use a black light source (UV) to show up possible molecular contaminants. Oils, greases, finger prints etc will show up under Black light inspection as fluorescence. Any evidence of fluorescence shall be cause for recleaning. If recleaning does not reduce the fluorescence, an investigation shall be made to determine whether the fluorescing material is contamination or the basic material
- Inspect the clean area walls and ceiling. If significant contamination is found, cover sensitive surfaces in the clean area with cleanroom bagging and proceed as indicated below
- Using a HEPA-filtered vacuum cleaner, vacuum the cleanroom walls and ceiling, making sure that all loose particles are removed from recesses and corners. Pay particular attention to the surfaces of the cleanroom gas supply pipes and test equipment cabling
- Vacuum the cleanroom floor in overlapping strokes
- Vacuum all areas under clean benches and laminar flow benches. Once all areas have been vacuumed start the wet cleaning process
- Two wheeled cleaning buckets are supplied for cleaning the MSSL cleanroom. In the first clean bucket, mix a solution of filtered DI water and non-ionic cleanroom detergent (follow the detergent dilution instructions). In the second clean bucket fill only with DI water. This second bucket is used to rinse contaminants from the mop prior to rinsing in the filtered DI water and non-ionic cleanroom detergent (first bucket) This two bucket method ensures that contaminants picked up on the mop are not redistributed to the cleanroom floor
- With the sponge mop and cleaning solution, start cleaning the floor from the HEPA filter end and work your way back to the entrance. Use a “pull and lift” method with the mop, stroking in one direction only. Rinse the mop after three cleaning strokes. Replace both the DI water and liquid cleaning solution when mop rinses fail to remove all visible contaminants from the mop
- Check tacky mats for cleanliness every day. If visible footsteps cover the mat area or the mat has otherwise lost adhesion, peel back the top layer
©MSSL
Created by Alex Rousseau last
modified:
February 4, 2004 16:12
|